Fall prevention, not just protection
Want to provide a safe working situation?
Together we can determine the best options for a guaranteed safety.
Contact usWorking at a height has become increasingly safer over the past few years. One example is the increased use of safety cages. Unlike safety belts, which protect just one individual against falling, safety cages aim to protect everyone accessing the working area. The primary goal of safety cages is to prevent someone from falling. Experience shows that in most cases it is sufficient for someone to have a support when losing their balance to prevent a fall. This has resulted in the latest European guideline ‘Working at height’, which has the following guidelines:
- Reducing the risk as much as possible (risk analysis, education, working instructions)
- Install collective protection (safety cages, folding stairs)
- Install individual protection (safety harness, personal protection).
Folding stairs with fixed safey cages allow operators to work on top of trucks/rail cars. These safety cages provide the final link between a safe working area and full maneuverability, as they do not limit the operator in his movements. There are numerous situations where operators have to cover the complete length of the truck/railcar to reach several manholes. For these situations, Wiese Europe has developed safety cages up to 12m in length which can be lowered from the roof or hinged at the platform walkways.
The safety cages are operated pneumatically or hydraulically depending on the facilities onsite. Numerous accessories are available to optimise safe working circumstances in the safety cages. There are movable doors to cover different lengths of trucks and small ‘drop-down’ fences at the side of the safety cage prevent the operator from sliding between the truck and the safety cage. One tank cleaning and repair company situated in the port of Antwerp has installed nearly 30 safety cages this year alone.
Loading arms
Flexible hoses used to be the standard for the loading/unloading operation in refineries and chemical plants in the past. But now the focus is moving over towards loading arms. Loading arms can be used for truck/railcar applications as well as for marine applications.
Land loading arms
Land loading arms form the most reliable alternative to flexible hoses when considering loading applications. As the main goal by liquid and gas transfers is to prevent contact between the product and the environment, land loading arms transcend flexible hoses in terms of handling and durability. The heart of loading arms, the swivel joint, can be adapted to virtually any loading situation with options such as FDA approved grease, heating and insulation, or PTFE-lining.
Land loading arms use a balancing system that can consist of spring cylinders or counterweights to minimise the effort to be borne by the operator. These spring cylinders and counterweights are maintenance free, and still adjustable should operating conditions change during the lifetime of the arm. These balancing systems can still be combined with a supporting gas spring for the last length (to compensate the extra weight of breakaway coupler or ball valve), or with hydraulic or pneumatic cylinders for operation. Loading arms can be customized to a specific loading operation with:
- Mechanical locking device,
- Suction hood,
- Overflow protection,
- Position detection,
- Vacuum breaker,
- Breakaway coupler,
- Shut off valve,…
Marine loading arms
Because of the size and the weight, all marine loading arms are counterweight-balanced. For the larger dimensions of marine loading arms this balancing is done by means of a pantograph system. Two pantograph systems can be distinguished by the manufacturers: the cable pantograph balancing system, or the rigid pantograph balancing system. Although both systems have their own advantages, the cable pantograph system remains the preferred model under the marine loading arm manufacturers. Its light weight construction, and lower maintenance requirements give it a considerable advantage over the rigid pantograph system, which uses more swivel joints and requires a heavier construction.
Although loading arms are constructed according the international guidelines of the OCIMF the piping construction can vary per model or application. For lighter applications/smaller sizes the product piping can be self supporting. For heavy duty applications and larger sizes there is frequently opted for a separate support structure which takes up the forces and loads, the product piping than is attached to this support structure and is only influenced by the product characteristics.
Self supporting model:
This model is balanced with a single rotating counterweight and due to its efficient design this arm can easily be manipulated by hand. The arm uses a self supporting structure so when balanced in a correct way, the product piping is the only part that needs to be brought into motion. When adding several options on this model, making it heavier and requiring more counterweights, hydraulic operation is also available for this model.
Separate support structure model:
This model uses a separate support structure making it perfectly suitable for the larger sizes and heavy duty tasks. It allows maintenance without dismantling the arm. All swivel joints are easy accessible and seals can be replaced with the loading arm in maintenance position. Although hand operated models are available, most manufacturers advise this model to be operated hydraulic because of the extra weight generated by the separate support structure. On marine loading arms a wide range of accessories is available to even more improve an ergonomic and smooth operation. These options include Emergency Release Systems, Quick Connect Disconnect Couplers (manual and hydraulic operated), but also a support jack and central greasing systems.
What can we do for you?
Check this out
Read more news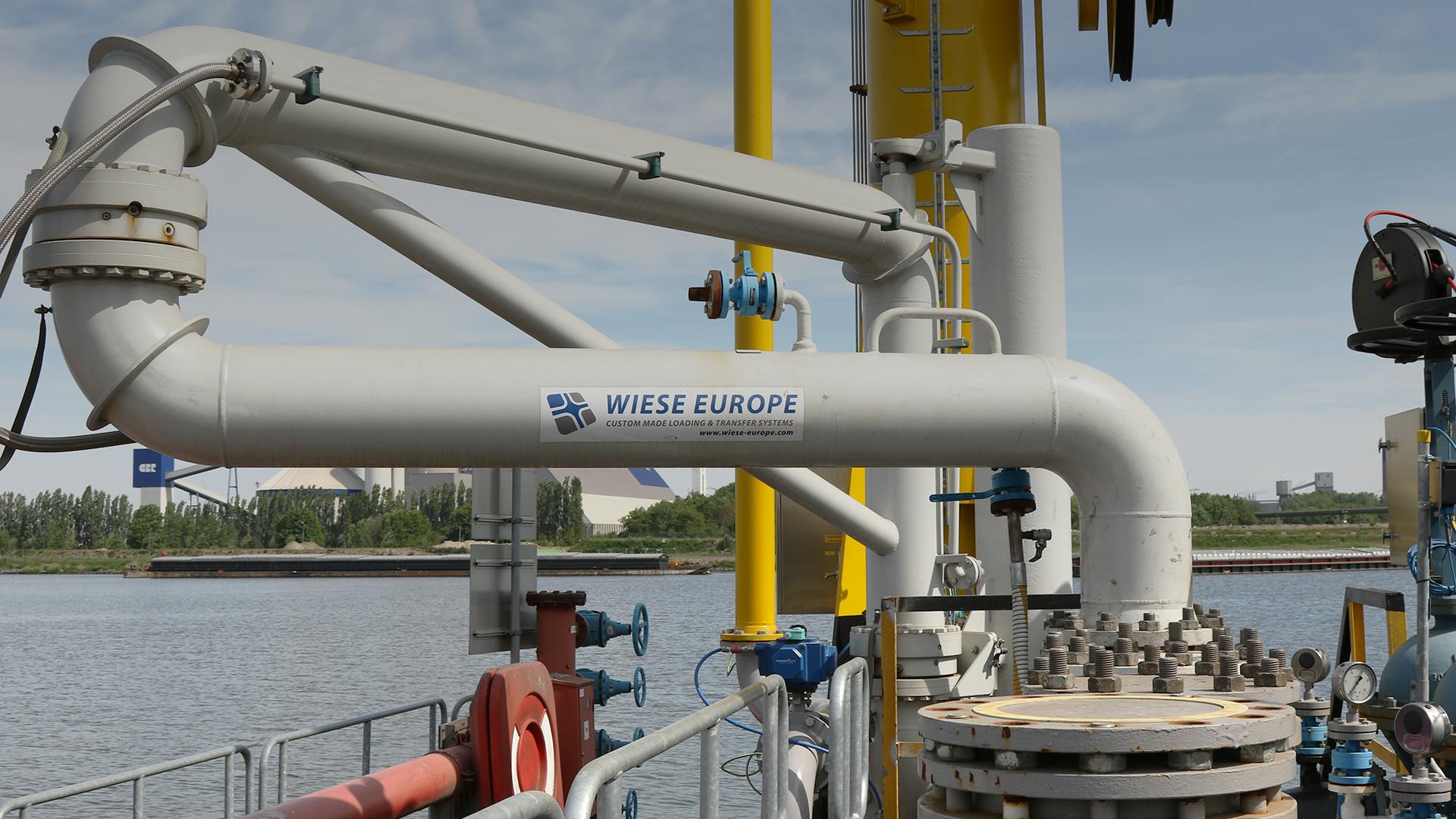
Wiese Europe: five values, one vision
In 1988 Chris Jacobs founded Wiese Belgium. But whose are the faces behind Wiese Europe today? What is their purpose and how do they envision the future? And how are they working today, more than thirty years after the foundation? Read moreWiese Europe: five values, one vision
Veilige pneumatica en hydraulica voor (scheeps)laadarmen en klaptrappen
Wiese Europe in het Kempense Brecht (Sint-Job-in-‘t‑Goor) maakt laad- en lossystemen voor de transfer van gassen en vloeistoffen. Het bedrijf bouwt zelf laadarmen en staat ook in voor de constructie van collectieve valbeveiliging zoals klaptrappen en veiligheidskooien waarmee het laden en lossen veilig kan verlopen. Hiervoor is het gebruik van pneumatica en hydraulica cruciaal. Read moreVeilige pneumatica en hydraulica voor (scheeps)laadarmen en klaptrappen
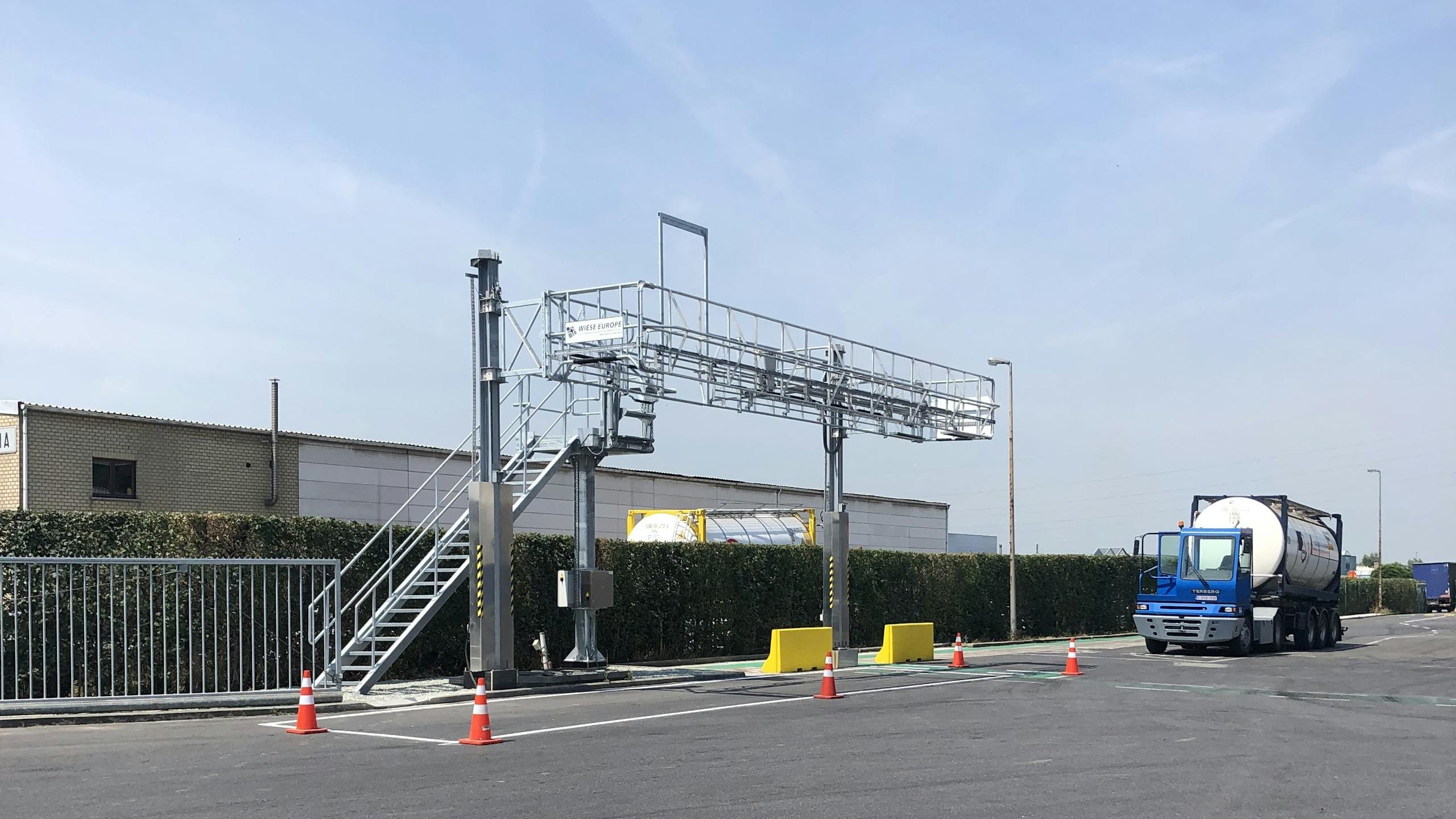